Screws in rotors are used to secure and fasten the rotor to the axle or hub, ensuring that the rotor stays in place and rotates with the wheel. This is essential for the proper functioning of the braking system and overall vehicle safety.
Without these screws, the rotor could become loose or misaligned, leading to brake performance issues and potential safety hazards. Rotors are a critical component of a vehicle’s braking system, responsible for slowing and stopping the vehicle when the brakes are applied.
They work in conjunction with the brake pads to generate friction and dissipate heat. To perform this function effectively, the rotors must be securely attached to the wheel hub. This is where the screws come in, providing the necessary stability and ensuring that the rotor rotates smoothly along with the wheel. Understanding the purpose of these screws is important for maintaining proper brake function and ensuring vehicle safety.
Understanding Screws
Screws in rotors play a crucial role in securing components and maintaining structural integrity during operation. They provide stability and prevent parts from loosening, ensuring smooth and efficient rotor function. Understanding the function of screws is essential for optimizing rotor performance and reliability.
Screws play a crucial role in the functionality of rotors. They are used to secure various components in place, ensuring the rotor operates smoothly and efficiently.
An Overview Of Screws
Screws in rotors serve as fasteners that help hold the rotor components together securely, preventing any unnecessary movement or disruptions during operation.
Types Of Screws Used In Rotors
- Machine Screw: Commonly used in rotors for their sturdy construction and ability to withstand high levels of stress.
- Set Screw: Ideal for providing a secure grip and alignment for specific rotor components.
- Self-Tapping Screw: Used for creating new threads within the rotor material, making installation easier.
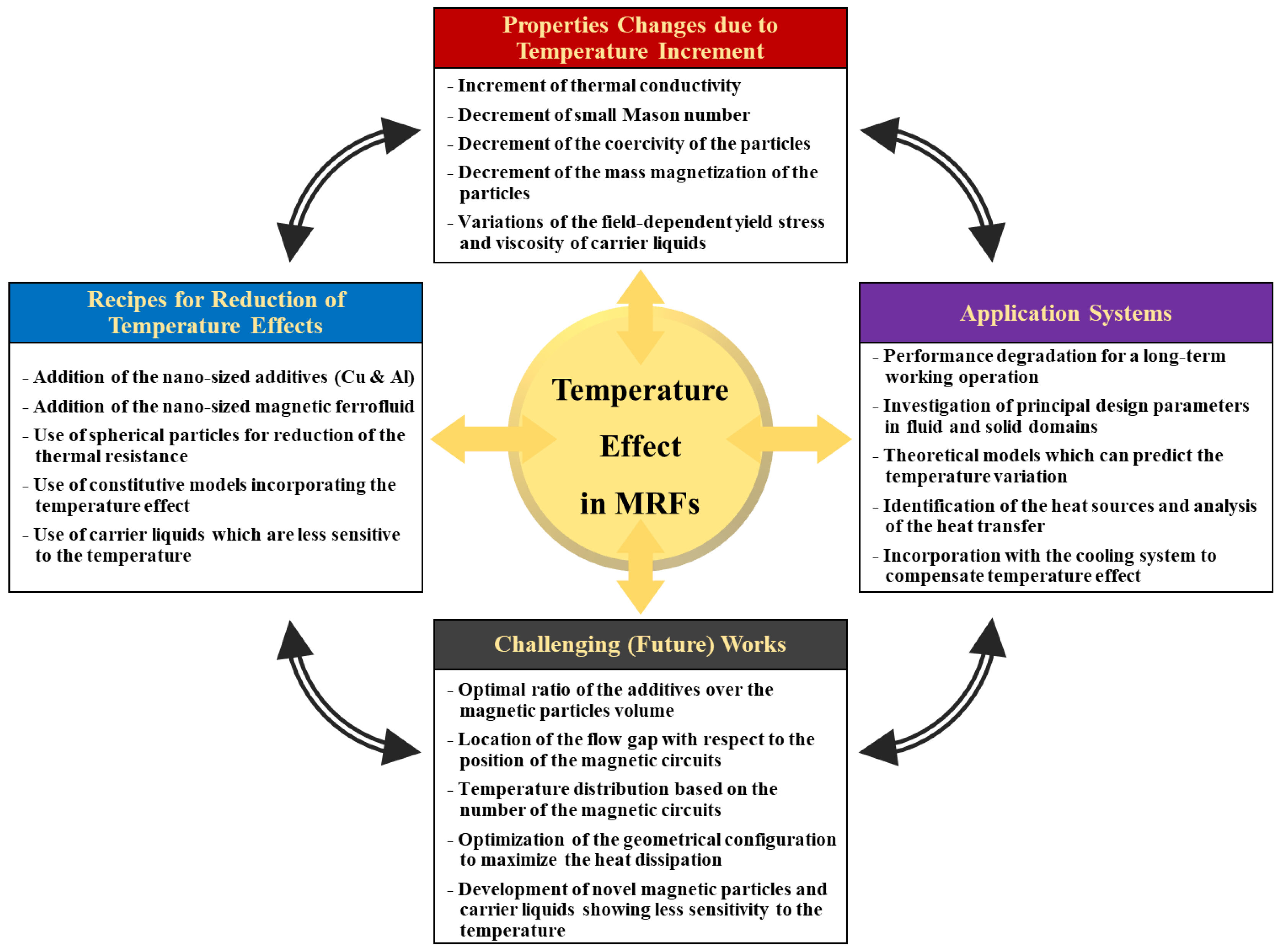
Credit: www.mdpi.com
Importance Of Screws In Rotors
Screws in rotors play a crucial role in the overall functionality of mechanical systems. They are essential in ensuring the stability and performance of rotors, making them an indispensable component in various applications.
Enhancing Stability
By securely fastening rotors in place, screws help prevent unwanted vibrations and ensure smooth operation.
Improving Performance
- Screws contribute to precise alignment, reducing friction and enhancing efficiency.
- Properly installed screws aid in maintaining balance and preventing potential malfunctions.
Factors To Consider When Choosing Screws
When it comes to rotors, choosing the right screws is crucial to ensure optimal performance and long-lasting durability. Several factors need to be considered when selecting screws for rotors:
Material
The material of the screw plays a significant role in its performance and resistance to wear and tear. Stainless steel screws are commonly used due to their corrosion resistance and strength. They provide excellent durability and reliability, making them ideal for rotors subject to heavy loads and harsh operating environments. Additionally, stainless steel screws can withstand high temperatures, making them suitable for applications that involve heat. On the other hand, titanium screws offer exceptional strength-to-weight ratio and are often preferred in lightweight rotor systems.
Thread Design
The thread design of screws determines their ability to effectively secure the rotor components. Different thread patterns and styles provide varying levels of grip and stability. For rotors, it is crucial to choose screws with a precise fit to ensure a secure connection between the rotor and its related parts. Threads that are too loose can lead to vibrations and potential malfunction, while overly tight threads may cause damage to the rotor or strip the threads altogether. The most commonly used thread designs for rotors include standard machine threads, self-tapping threads, and lag threads.
Length And Diameter
Choosing the appropriate length and diameter of screws is essential for ensuring that the rotor components are properly fastened together. Using screws that are too short may compromise the strength and stability of the rotor assembly, leading to potential accidents or failures. On the other hand, excessively long screws can interfere with the functionality of other components or create unnecessary weight. It is important to accurately measure the required length and diameter based on the specific rotor design and assembly requirements. This guarantees a snug and secure fit without any compromise in performance.
Installation And Maintenance Of Screws
In the context of rotors, screws play a critical role in ensuring the proper installation and maintenance of the components. Properly installed and maintained screws are vital for the efficient performance and longevity of rotors. Focusing on the subheading of “Installation and Maintenance of Screws,” we will delve into proper techniques for installation as well as the importance of regular inspection and replacement.
Proper Installation Techniques
Proper installation of screws within rotors is essential to ensure the secure and stable attachment of the components. During installation, it is imperative to align the screws correctly with the designated holes to prevent any misalignment issues. Additionally, using the appropriate torque to fasten the screws is crucial to avoid under-tightening or over-tightening, which can lead to potential damage or performance issues.
Regular Inspection And Replacement
Regular inspection of screws is imperative to identify any signs of wear, damage, or corrosion. Scheduled maintenance should include checking for loose or missing screws, as well as assessing the overall condition of the fasteners. Any indication of wear or degradation should prompt immediate replacement to prevent performance issues or potential hazards. By adhering to a regular inspection and replacement schedule, the integrity and functionality of the rotors can be effectively maintained.
Common Issues With Screws In Rotors
Rotors play a vital role in the braking system of vehicles and machinery. The screws in rotors are essential to ensure the stability and proper functioning of the rotor assembly. However, several common issues can arise with these screws, leading to potential safety hazards and decreased performance. Understanding these issues is crucial for maintaining the effectiveness of the braking system.
Loose Or Damaged Screws
Loose or damaged screws in rotors can pose a significant risk to the braking system’s integrity. When screws become loose, they can result in increased rotor play and contribute to uneven braking, leading to potential accidents and reduced control of the vehicle or machinery. Damaged screws, on the other hand, can compromise the structural integrity of the rotor assembly, raising concerns about its ability to withstand the forces exerted during braking.
Corrosion
Corrosion is a prevalent issue affecting screws in rotors, especially in environments with high moisture or salt exposure. Corrosion weakens the screws, making them susceptible to breakage or failure under stress. Additionally, corroded screws can lead to uneven pressure distribution, causing juddering and vibration during braking, which affects the overall performance and safety of the braking system.
Thread Stripping
Thread stripping, often caused by improper installation or overtightening, can significantly impact the functionality of screws in rotors. When the threaded portion of the screws becomes stripped, their ability to secure the rotor assembly is compromised, potentially leading to rotor displacement and diminished braking efficiency. Identifying and addressing thread stripping issues is crucial for maintaining the structural integrity of the rotor assembly.

Credit: www.amazon.com
Tips For Maximizing Screw Performance
Optimizing screw performance in rotors is crucial for efficiency. Proper tightening and regular maintenance ensure optimal functionality and prevent potential issues. Implementing correct installation techniques is key for maximizing screw performance and extending rotor lifespan.
Applying Correct Torque
Screws play a vital role in the performance of rotors. Applying the correct torque is crucial to ensure the screws are securely tightened. Insufficient torque can result in loose screws, which can lead to rotor imbalance and potential damage to the system. On the other hand, excessive torque can cause stress on the rotor and its components, reducing overall performance and lifespan.
When applying torque to screws, it is important to use a torque wrench and follow the manufacturer’s specifications. This ensures that the screws are tightened to the appropriate level and eliminates the risk of over or under-tightening. It is also important to periodically check the screws to ensure they remain properly torqued over time.
Using Locking Mechanisms
In addition to applying correct torque, using locking mechanisms further enhances the performance of screws in rotors. Locking mechanisms such as thread-locking adhesives or nylon locking patches provide an additional layer of security and prevent loosening due to vibrations or external forces.
Whether it’s a high-speed rotor or a heavy-duty application, utilizing locking mechanisms can significantly reduce the chances of screws becoming loose and compromising the rotor’s efficiency. Furthermore, these mechanisms help in maintaining consistent torque values, ensuring long-term stability and reliability.
Periodic Lubrication
Periodic lubrication is another essential factor for maximizing screw performance in rotors. Lubricants reduce friction between the screws, facilitating smooth rotation and preventing excessive wear and tear. This not only extends the lifespan of the screws but also contributes to the overall efficiency of the rotor.
It is recommended to use lubricants specifically designed for rotor screws, as they provide key properties such as resistance to high temperatures and corrosion. Regular lubrication intervals should be followed, as specified by the manufacturer, to ensure optimal performance and minimize the risk of premature screw failure.

Credit: www.amazon.com
Conclusion
Screws play a crucial role in rotors by securely fastening different components together. They provide stability and enable smooth rotation, ensuring optimal performance and safety. By understanding the purpose of screws in rotors, manufacturers can design and build more efficient systems.
So, whether in industrial machinery or everyday appliances, the use of screws in rotors helps create reliable products that meet the needs of various industries.