Yes, new brake drums need to be turned to ensure they are properly machined and in optimal condition for safe operation. It is vital to have new brake drums turned to guarantee proper contact and friction with the brake shoes, preventing any potential issues with braking performance.
When it comes to vehicle safety, the condition of your brake system is critical. The brake drums play a crucial role in providing the necessary friction for the brake shoes to operate efficiently. Turning new brake drums before installation helps to eliminate any imperfections and ensures a smooth and reliable braking experience.
This maintenance procedure is essential for optimal performance and safety, as it promotes even wear on the brake shoes and prevents potential issues such as brake pulsation or noise. By following this practice, you can maintain the integrity of your vehicle’s braking system and ensure a safe driving experience.
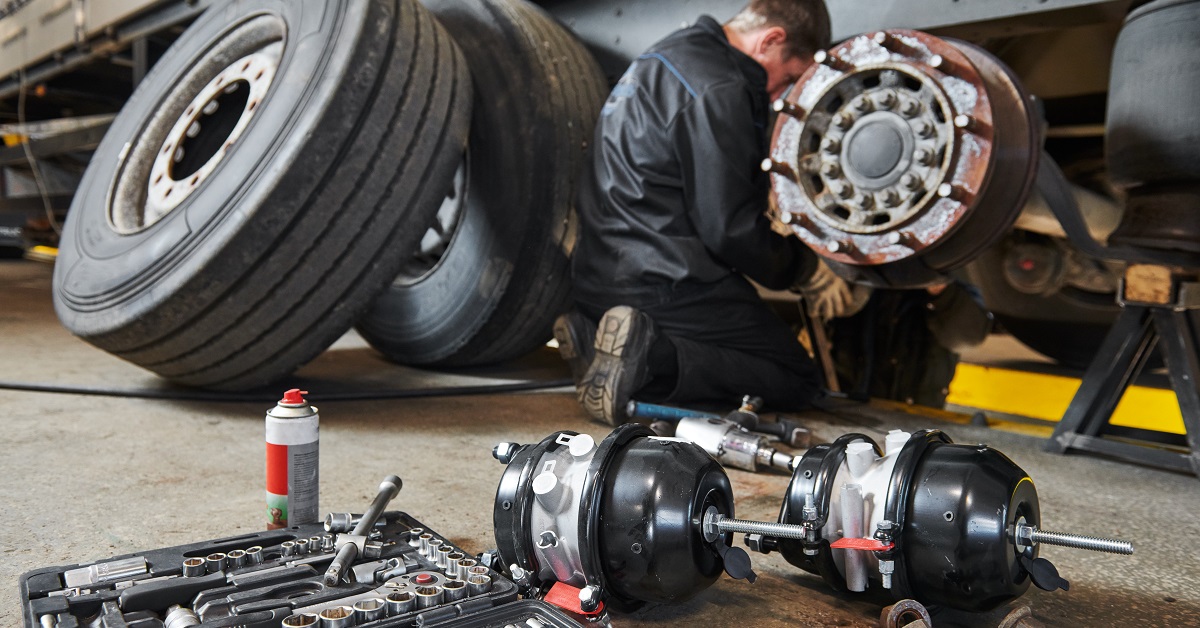
Credit: stearnscompanies.com
Why Brake Drum Turning?
Brake drum turning is essential for maintaining your vehicle’s braking system performance. This process involves machining the surface of the brake drum to restore its smoothness and roundness. By turning brake drums, you can ensure optimal contact between the brake pads and drums, leading to improved stopping power and overall safety. Let’s explore the reasons why brake drum turning is crucial for your vehicle.
Signs Of Brake Drum Wear
1. Uneven wear patterns on the brake drums
2. Excessive grooving or scoring on the drum surface
3. Vibration or pulsation during braking
4. Reduced braking efficiency
Benefits Of Brake Drum Turning
1. Restores smooth braking surface
2. Improves brake pad longevity
3. Enhances braking performance
4. Ensures even distribution of braking force
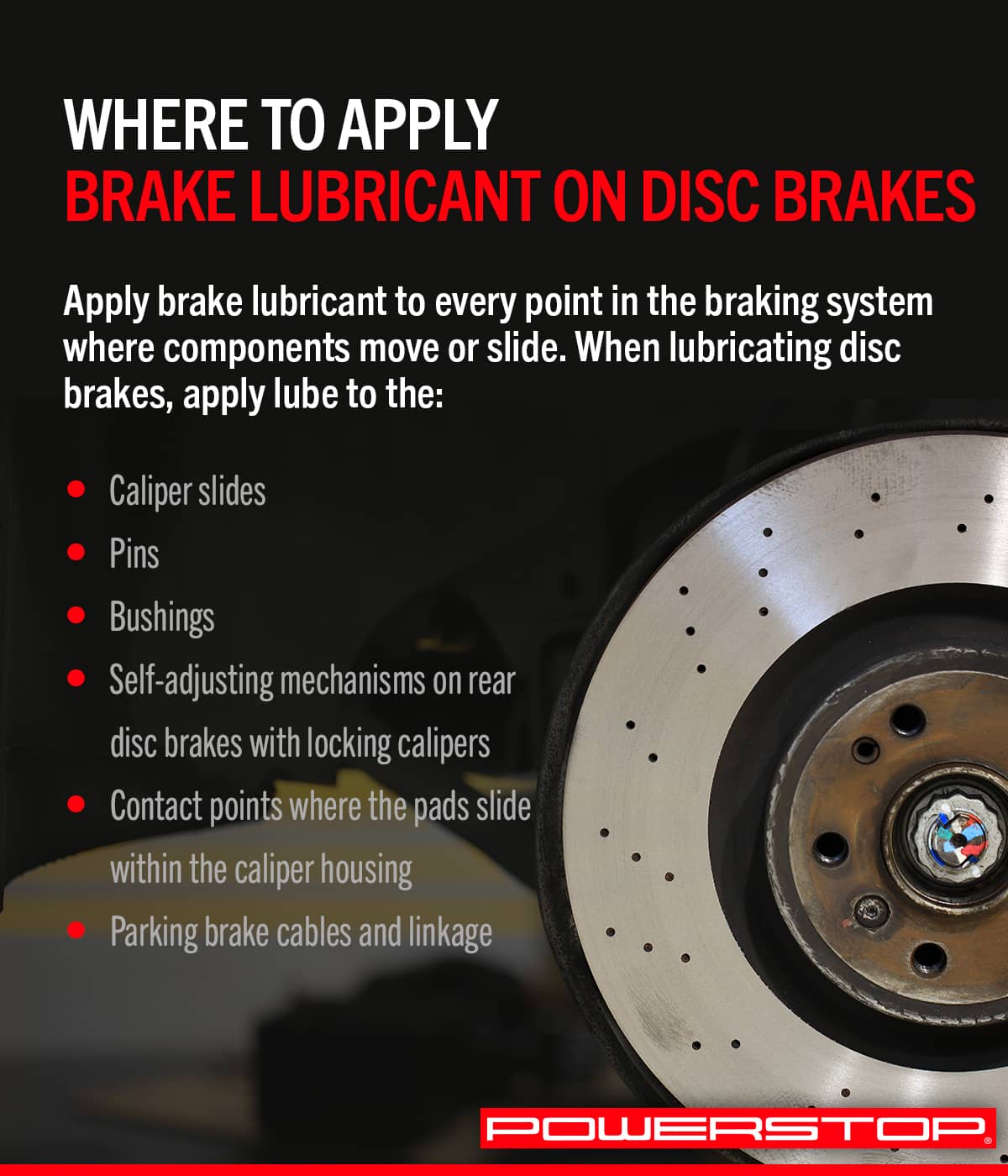
Credit: www.powerstop.com
When Should Brake Drums Be Turned?
Brake drums should be turned if they show signs of wear, such as scoring or grooving. It’s not always necessary to turn new brake drums, but it’s important to inspect them for imperfections before installation. Turning brake drums can help ensure proper brake performance and longevity.
Mileage Or Time Intervals
Maintaining brake drums is essential for safe driving. Experts recommend turning brake drums every 50,000 miles.
Signs Of Brake Performance Issues
If you notice vibration or pulsation when braking, it’s a sign that brake drums might need turning.
Understanding Brake Drum Turning Process
Brake drum turning is an essential process to ensure the smooth operation of your vehicle’s braking system. Over time, brake drums can become worn, warped, or corroded, which can negatively impact their performance. Turning the brake drums is a cost-effective way to restore their functionality without the need for a complete replacement. In this article, we will provide an overview of the brake drum turning process, the tools and equipment needed, and a step-by-step guide.
Overview Of Brake Drum Turning
Brake drum turning involves machining the surface of the drum to restore its smoothness and remove any imperfections. This process is performed on a lathe machine, which rotates the brake drum while a cutting tool shaves off a thin layer of the drum’s surface. By doing so, any irregularities in the drum’s surface are eliminated, ensuring proper contact between the brake shoes and the drum. This improves braking performance, reduces noise, and prevents brake pedal pulsation.
Tools And Equipment Needed
To turn brake drums, you will need the following tools and equipment:
- Lathe machine: This is the primary tool used to perform the drum turning process. Make sure the lathe machine is in good working condition and properly calibrated.
- Brake drum adapter set: These adapters are necessary to securely mount the drum on the lathe machine. Different adapters are available to fit various drum sizes.
- Cutting tool: This is the part of the lathe machine that removes the thin layer from the drum’s surface. Ensure that the cutting tool is sharp and suitable for brake drum turning.
- Measuring tools: You will need a micrometer or a dial indicator to measure the drum’s thickness after turning to ensure it is within the manufacturer’s specifications.
- Safety equipment: Always wear protective goggles and gloves to prevent any injuries while operating the lathe machine.
Step-by-step Guide
Here is a step-by-step guide to turning brake drums:
- Secure the lathe machine: Ensure the lathe machine is properly fixed to a stable surface to prevent any movement during operation.
- Select the appropriate brake drum adapter: Choose the adapter that matches the size and type of brake drum you are going to turn. Attach the adapter securely to the lathe machine.
- Mount the brake drum: Install the brake drum on the adapter, ensuring it is centered and tightly secured using the proper mounting bolts or clamps.
- Set the cutting tool: Adjust the cutting tool to the correct depth and position, ensuring that it will remove the desired amount of material from the drum’s surface.
- Turn the drum: Start the lathe machine and slowly rotate the drum while engaging the cutting tool. Allow the machine to complete several passes to achieve a smooth and even surface.
- Measure the drum: After turning, use a micrometer or dial indicator to measure the drum’s thickness. Ensure it meets the manufacturer’s specifications.
- Finish the process: If the drum passes the measurements, remove it from the lathe machine and clean any metal shavings or debris. Reinstall the drum on the vehicle along with new brake shoes.
By following these steps, you can effectively turn your brake drums, restoring their performance and extending their lifespan. Remember, if you are unsure or inexperienced, it is recommended to consult a professional mechanic to ensure the process is done correctly.
Factors To Consider Before Deciding To Turn Brake Drums
Factors to Consider Before Deciding to Turn Brake Drums
Extent Of Wear
Inspecting the extent of wear on your brake drums is crucial in determining whether they need to be turned. Signs of wear such as deep scoring, heat cracks, or an uneven surface may indicate that turning the brake drums is necessary. If the wear is within tolerances and the surface is smooth, turning may not be required.
Manufacturer’s Recommendations
Refer to the manufacturer’s specifications and recommendations for your vehicle model. Some manufacturers may specify the maximum allowable diameter for brake drums, and whether they can be turned. Adhering to these guidelines ensures the safety and performance of your braking system.
Cost Comparison With Replacement
When considering whether to turn brake drums, it’s essential to compare the costs with replacement. Turning brake drums may be a cost-effective option if the drums are within specifications and the wear is not severe. However, if the drums are heavily worn or damaged, replacement may be the more practical and safer choice.
Finding A Qualified Brake Drum Machinist
Qualified brake drum machinists are essential for accurate turning of brake drums. While new brake drums might not always require turning, a skilled machinist can determine the best course of action to ensure optimal performance and safety. Trusting a professional with this task can save time and money in the long run.
Importance Of Professional Expertise
When it comes to brake drum machining, professional expertise is crucial. A qualified machinist ensures that the brake drums are restored to optimal condition, enhancing the safety and performance of the vehicle. The expertise of the machinist directly impacts the effectiveness of the brake system, making it imperative to entrust this task to a knowledgeable professional.
Qualifications To Look For
Seeking a machinist with the right qualifications is essential. Look for professionals with certifications or training in brake system repair and machining. Additionally, experience in working with a variety of vehicles and brake drum types is a valuable qualification to consider. This ensures that the machinist understands the nuances of different braking systems and can provide comprehensive services.
Seeking Recommendations
One effective way to find a skilled brake drum machinist is by seeking recommendations. Ask for referrals from other vehicle owners, local mechanics, or automotive enthusiasts. Hearing about positive experiences directly from those who have utilized the services can provide valuable insights into the proficiency of the machinist. Moreover, online reviews and feedback can aid in making an informed decision.
Avoiding Common Brake Maintenance Mistakes
When it comes to brake maintenance, there are certain mistakes that can lead to costly repairs or even accidents. By avoiding these common brake maintenance mistakes, you can ensure the safety and performance of your vehicle for years to come.
Skip Routine Brake Inspections
Skipping routine brake inspections is one of the most common mistakes car owners make. Regular brake inspections are essential to catching and resolving issues before they become major problems. Ignoring these inspections can compromise the effectiveness of your brakes and put you at risk on the road.
During a routine brake inspection, a qualified technician will examine the brake pads, brake calipers, brake lines, and brake fluid for any signs of wear or damage. This helps to identify any potential issues and allows for timely repairs or replacements, ensuring your brakes are working optimally.
Ignore Brake Warning Signs
Ignoring brake warning signs is another mistake that can have serious consequences. Your vehicle’s braking system is designed to give you warning signs when it needs attention. It’s crucial not to ignore these signs and address them promptly to prevent further damage and maintain your safety.
Some common brake warning signs include squeaking or grinding noises, vibrations while braking, a spongy brake pedal, or a dashboard warning light. These signs indicate that there may be a problem with the brake pads, rotors, or other components. Ignoring these signs can lead to excessive wear and tear, decreased braking performance, and potential brake failure.
Use Inferior Quality Parts
Using inferior quality parts is a mistake that can compromise the overall performance and durability of your brakes. While it may be tempting to opt for cheaper options, it’s important to choose high-quality brake components to ensure their effectiveness and longevity.
When replacing brake pads, rotors, or other brake components, make sure you invest in reputable brands that meet or exceed the manufacturer’s specifications. Using inferior quality parts can result in poor braking performance, increased stopping distances, and even premature brake failure, putting you and your passengers at risk.
Warning Sign | Description |
---|---|
Squeaking or Grinding Noises | High-pitched squeaking or grinding noises when applying the brakes, indicating worn brake pads |
Brake Pedal Vibrations | Shaking or pulsating brake pedal while braking, suggesting uneven brake rotor wear |
Spongy Brake Pedal | Brake pedal feels soft or sinks to the floor when pressed, indicating air in the brake lines |
Dashboard Warning Light | Indicator light on the dashboard illuminates, signaling a potential brake system malfunction |
By paying attention to these warning signs and addressing them promptly, you can avoid costly repairs and ensure the safety of your vehicle.
To conclude, it’s essential to avoid common brake maintenance mistakes such as skipping routine inspections, ignoring warning signs, and using inferior quality parts. By prioritizing proper brake maintenance, you can drive with confidence, knowing that your vehicle’s braking system is in optimal condition.
Alternative Solutions To Brake Drum Turning
When it comes to brake maintenance, it’s essential to explore alternative solutions to brake drum turning to save time and money while ensuring optimal performance.
Brake Drum Replacement
Consider replacing worn-out brake drums with new ones to maintain brake efficiency and safety.
Upgrading To Slotted Or Drilled Brake Rotors
Upgrade to slotted or drilled brake rotors for improved heat dissipation and better performance during braking.
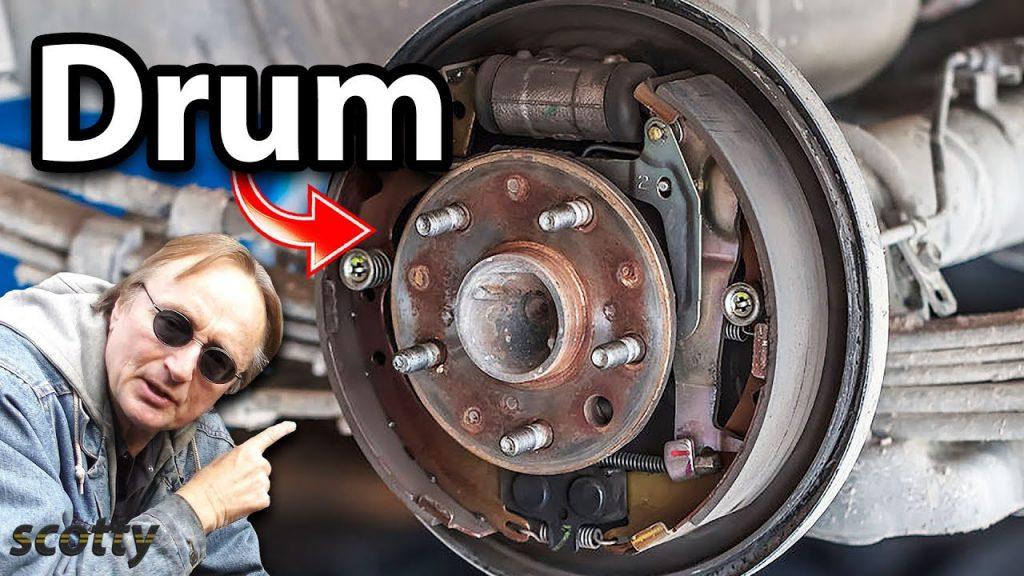
Credit: carfromjapan.com
Maintaining Healthy Brake System For Optimal Performance
To ensure optimal performance, it is important to maintain a healthy brake system by evaluating if new brake drums need to be turned. This step can significantly enhance braking efficiency and safety on the road. Regular inspections and proper maintenance are key to prolonging the life of your brake system.
Maintaining an optimal brake system is crucial for safe driving. Regular cleaning and lubrication prevent wear and maximize efficiency. Proper break-in procedures ensure longevity of the brake drums.Regular Cleaning And Lubrication
Regular cleaning and lubrication reduce friction and enhance brake performance.Proper Break-in Procedures
Proper break-in procedures eliminate impurities for smooth braking experience. Maintenance is key to ensuring safety. Neglecting care can result in costly repairs. A well-maintained brake system is crucial for vehicle safety. Brake system regular inspection is essential for optimal performance.Conclusion
Brake drums play a crucial role in the braking system of a vehicle. While it is not always necessary to turn new brake drums, it is recommended to do so in certain situations. By ensuring the drums are properly turned, you can optimize performance and extend the lifespan of your brakes.
Keep in mind the manufacturer’s recommendations and consult with a professional mechanic for the best course of action.