Brake drums are critical components of a vehicle’s braking system, responsible for providing friction to slow or stop the vehicle. They work by using shoes to press against the inside of the drum, generating friction and heat. Over time, brake drums can wear out or get damaged, and drivers often wonder if they can be welded to repair the damage. Welding may seem like a straightforward solution to fix a broken brake drum, but is it safe or effective? In this article, we will explore whether brake drums can be welded, the potential risks, and alternative methods for repairing or replacing damaged brake drums.
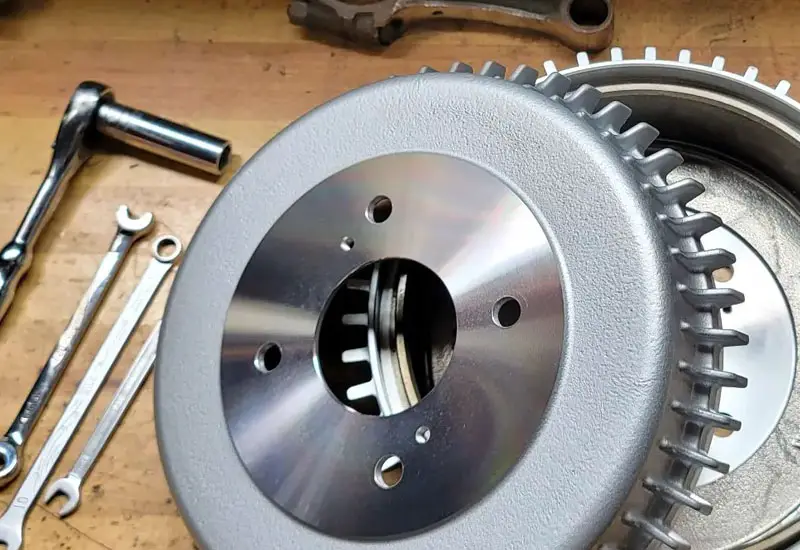
Understanding Brake Drums and Their Function
Before discussing the possibility of welding brake drums, it’s essential to understand their function and why they are crucial for vehicle safety. Brake drums are part of a drum brake system, typically found on older vehicles or on the rear axles of certain vehicles.
The Role of Brake Drums in the Braking System
Brake drums are attached to the wheel hub and rotate along with the vehicle’s wheels. When the driver applies the brakes, brake shoes inside the drum press against its inner surface, creating friction. This friction slows down the rotation of the wheel and, ultimately, brings the vehicle to a stop.
The friction generated during braking causes the brake drum to heat up. The design of the brake drum allows for heat dissipation, which helps prevent overheating and maintains braking efficiency. Over time, however, repeated use can cause wear and tear on the drum’s surface, which can lead to grooves, cracks, or warping.
Why Brake Drums Get Damaged
Brake drums can be damaged for various reasons, including:
- Excessive Heat: Constant braking can generate high temperatures, which can cause the drum to warp or crack.
- Wear and Tear: Brake drums wear down as the brake shoes press against them repeatedly.
- Corrosion: Brake drums are exposed to moisture, dirt, and road salts, which can cause rust and corrosion.
- Impact Damage: Road debris, accidents, or poor handling during repairs can cause physical damage to the brake drum.
When brake drums become damaged, the braking performance of the vehicle can be compromised, leading to reduced safety. This is why many vehicle owners wonder if welding the brake drum can provide a quick fix.
Can Brake Drums Be Welded?
Now that we have a basic understanding of brake drums, the next step is to address whether welding can be an effective way to repair them. Welding involves joining metal parts by heating them to their melting point, allowing the material to fuse together. However, brake drums are typically made of cast iron or steel, which presents challenges when it comes to welding.
The Challenges of Welding Brake Drums
- Cast Iron Properties: Most brake drums are made of cast iron, which is a brittle material. Welding cast iron requires special techniques, as it can crack easily due to thermal stresses during the welding process.
- Heat Management: Brake drums experience extreme heat during braking, and welding can alter the material’s properties, leading to weakness or distortion.
- Precision Required: Brake drums need to be precisely machined to maintain proper braking performance. Welding can distort the shape, leading to imbalanced drums and reduced braking efficiency.
Why Welding Brake Drums Is Not Recommended
Welding brake drums is generally not recommended due to several factors.
- Weakening the Metal: Welding causes localized heating of the metal, which can alter the material’s strength. Since brake drums are subjected to high-stress levels and intense heat, altering their structural integrity through welding can lead to catastrophic failure during use.
- Cracking and Distortion: Cast iron is prone to cracking during welding due to thermal expansion and contraction. Even if the welding is successful, the heat generated during the process can cause the drum to warp or distort, making it ineffective for use.
- Imbalanced Surface: Brake drums must have a smooth and balanced surface to ensure uniform contact with the brake shoes. Welding can create bumps or uneven surfaces, leading to vibrations or poor braking performance.
- Safety Concerns: Given that brake drums play a critical role in stopping the vehicle, any compromise in their strength or functionality can jeopardize safety. For this reason, welding brake drums is seen as a risky and unreliable repair method.
Alternative Methods for Repairing Brake Drums
Instead of welding, several other methods can be used to repair or restore a damaged brake drum. These methods are generally safer and more effective in maintaining the drum’s integrity and performance.
1. Turning or Machining the Brake Drum
Turning the brake drum is a common method for restoring its surface. This involves using a machine to remove a thin layer of material from the inside of the drum, smoothing out any grooves or imperfections. By turning the drum, the surface is restored to a more even condition, which allows the brake shoes to make proper contact.
Turning is only effective if the brake drum is not excessively worn or cracked. There is a limit to how much material can be removed before the drum becomes too thin and weak to function properly. It’s also important to ensure that the brake drum is properly balanced after machining to prevent vibrations.
2. Brake Drum Resurfacing
Brake drum resurfacing is similar to turning but involves a more thorough process of removing material from the surface to restore its original condition. This method can help remove minor cracks, grooves, and surface damage. However, resurfacing should only be done on drums that are still within the manufacturer’s thickness specifications.
3. Replacing the Brake Drum
In many cases, replacing the brake drum is the most reliable solution. If the brake drum is severely damaged, cracked, or worn beyond the manufacturer’s specifications, welding, resurfacing, or turning may not be enough to restore its functionality. Replacing the brake drum with a new one ensures that the vehicle’s braking system remains safe and effective.
Brake drums are designed to last for a long time, but when they become too damaged, replacing them with high-quality parts is the best option for maintaining safety and performance.
Risks of Trying to Weld Brake Drums
While welding may seem like a quick and inexpensive fix, it comes with several risks that can compromise the safety and functionality of the braking system.
1. Compromised Brake Performance
Welding can alter the metal’s strength and integrity, potentially making the brake drum less effective at dissipating heat and creating friction. A weakened brake drum may not perform as well as a properly machined or replaced one, leading to reduced braking power and longer stopping distances.
2. Increased Risk of Cracks
The high heat involved in welding can cause existing cracks in the brake drum to worsen, leading to further damage. Even if the welding process is successful, the chances of cracks developing over time are much higher due to the changes in the material’s properties.
3. Distorted Shape and Surface
Welding can distort the shape of the brake drum, making it uneven or out of round. This can result in vibrations or poor contact between the brake shoes and the drum, leading to uneven braking performance and a rough ride. In the worst-case scenario, an imbalanced brake drum can cause brake failure.
4. Safety Hazards
Brake drums are a crucial component of the braking system. Any compromise in their structural integrity can lead to brake failure, which is a significant safety hazard. The risks of welding brake drums far outweigh any potential benefits, as it could lead to catastrophic failure in critical driving situations.
Should You Weld Brake Drums?
Given the risks and challenges associated with welding brake drums, it is highly recommended to avoid this method for repairs. While it might seem like a cost-effective solution, the long-term safety and performance of the vehicle’s braking system are far more important. Instead, consider options like turning, resurfacing, or replacing the brake drum for a more reliable and safe solution.
If you are unsure about the condition of your brake drums, it’s always best to consult a professional mechanic who can assess the damage and recommend the appropriate course of action. Repairing or replacing brake drums is an essential part of maintaining a safe and functional vehicle, and proper care should be taken to ensure that the braking system is always in top condition.
I hope this article has helped you understand why welding brake drums is not a recommended repair method. While welding might seem like a quick fix, it poses significant risks to the safety and performance of your vehicle. Instead, consider alternatives like resurfacing or replacing the brake drum to ensure that your braking system remains reliable and effective. Always prioritize safety when dealing with critical components like brake drums to keep your vehicle performing at its best.
Are These Questions in Your Mind?
Is it safe to weld a brake drum?
Welding a brake drum is not recommended due to the risk of weakening the metal, distorting the shape, and causing cracks. It can compromise braking performance and vehicle safety.
Can brake drums be resurfaced?
Yes, brake drums can be resurfaced using a lathe to remove a small amount of material from the drum’s surface, restoring its condition. This is only effective if the drum is not excessively worn or cracked.
Do I need to replace my brake drums if they are cracked?
Yes, if the brake drums are cracked or significantly damaged, replacing them is the safest option. Welding or resurfacing may not restore their integrity.
Can I turn my brake drums if they are warped?
If the brake drums are only slightly warped, they may be turned to restore their shape. However, if the warping is severe, the drums should be replaced.
Is it possible to repair a brake drum without replacing it?
Yes, brake drums that are mildly damaged can often be repaired through resurfacing or turning. However, severely damaged drums may need to be replaced.
Can I drive with worn-out brake drums?
Driving with worn-out brake drums can reduce braking efficiency and increase the risk of brake failure. It’s important to replace them if they no longer meet safety standards.
Is it necessary to balance brake drums after resurfacing?
Yes, after resurfacing, brake drums should be balanced to ensure smooth braking and to avoid vibrations during driving.
Do I need to replace both brake drums at the same time?
It’s recommended to replace both brake drums if one is damaged to ensure balanced braking. Replacing only one drum could lead to uneven braking performance.
Can I repair a brake drum myself?
While minor repairs like resurfacing may be possible with the right equipment, it’s best to have brake drums inspected and repaired by a professional mechanic to ensure proper safety and performance.
Is welding brake drums cheaper than replacing them?
While welding may seem cheaper, it is not a safe or effective solution. Replacing the brake drum may cost more initially but is a safer long-term investment.