Have you ever been driving and suddenly your engine feels like it’s struggling to keep up, or maybe your check engine light flickers on for no apparent reason? A common cause could be a problem with your crankshaft position sensor. And when that sensor runs into trouble—specifically a short circuit—it’s like the engine loses its sense of direction. But don’t worry! Repairing a short circuit in this sensor is something you can tackle, and I’ll guide you step by step. Let’s dive into how to repair a short circuit in the crankshaft position sensor, so you can get back on the road in no time!
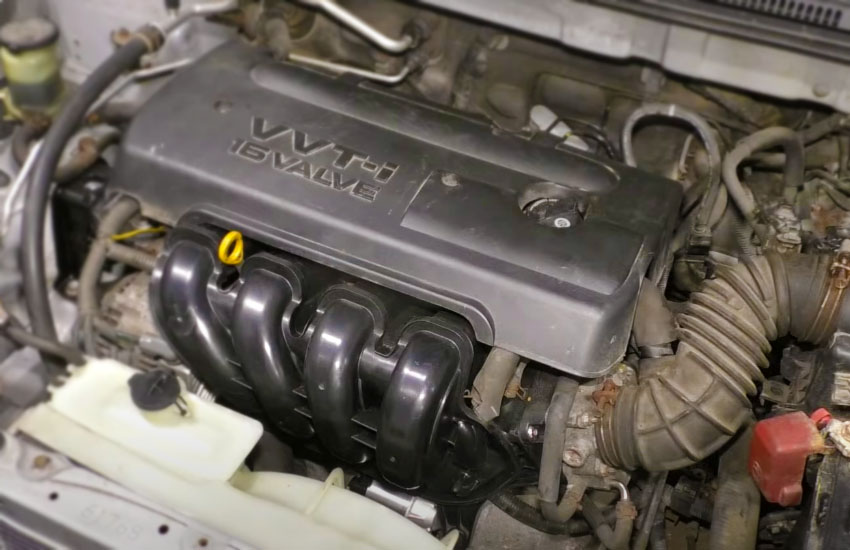
Understanding the Short Circuit in a Crankshaft Position Sensor
When it comes to diagnosing engine problems, the crankshaft position sensor is often the unsung hero. It keeps track of your engine’s rotation, which is essential for the timing of fuel injection and ignition. So, when this sensor runs into issues, the engine struggles to work properly.
A short circuit in the crankshaft position sensor can create serious problems, and you may notice issues like poor engine performance, stalling, or rough idling. But first, let’s break down what exactly a short circuit is and how it impacts your sensor.
What is a Short Circuit in the Crankshaft Position Sensor?
A short circuit happens when the electrical current in a circuit doesn’t flow the way it’s supposed to. In a crankshaft position sensor, a short circuit typically occurs when there is unintended contact between two wires or electrical components that shouldn’t be touching. This causes electrical signals to get confused or blocked, leading to a failure in communication between the sensor and the engine control unit (ECU). It’s like a game of telephone, but the message never gets through because the wires are crossed.
Common Causes of Short Circuits in the Sensor
Several factors can lead to a short circuit in your crankshaft position sensor. The most common culprits are:
- Damaged Wires: Over time, wires can get worn out, frayed, or exposed to elements like heat, moisture, and friction. If a wire is damaged, it can touch another wire or part of the engine, causing a short circuit.
- Corrosion: Salt, dirt, and moisture can corrode the sensor’s wiring connections, causing improper contact and shorts.
- Faulty Connections: Sometimes, the sensor or the wiring connections themselves may be poorly installed or loose, causing intermittent electrical contact that results in a short.
- Electrical Overload: If your engine’s electrical system gets overloaded due to a malfunctioning part, it could send too much voltage to the sensor, leading to a short circuit.
Symptoms of a Short Circuit in the Crankshaft Position Sensor
How do you know if your crankshaft position sensor has a short circuit? The symptoms can vary, but here are some key signs that something’s wrong:
- Check Engine Light: This is the most obvious symptom. If your crankshaft position sensor has a short, the ECU will usually trigger a check engine light.
- Poor Engine Performance: If you notice your engine sputtering, misfiring, or having trouble starting, it could be due to incorrect signals from the sensor.
- Stalling or Rough Idling: Since the crankshaft position sensor plays a huge role in engine timing, a faulty sensor can cause your engine to stall or idle roughly.
- Difficulty Starting: A short-circuited sensor might prevent the engine from starting altogether, as it disrupts the fuel injection and ignition timing.
If you’re seeing these signs, it’s time to take a closer look at your crankshaft position sensor and figure out whether there’s a short circuit causing the trouble.
Step-by-Step Guide to Diagnosing the Issue
Diagnosing a short circuit in your crankshaft position sensor may sound intimidating, but I promise, it’s much more manageable than it seems! This process involves a few essential tools—like a multimeter—and some patience, but with the right approach, you can do it yourself. Let’s walk through the steps of diagnosing the issue.
Gather Your Tools
Before you begin, make sure you have everything you need:
- Multimeter: This tool helps you measure the electrical current and resistance in the wiring and sensor. It’s a must-have for diagnosis.
- Wrenches and Socket Set: You may need these to remove the sensor and gain access to the wiring.
- Replacement Parts: If you find any damaged wiring or if the sensor is faulty, be ready to replace it.
- Work Gloves and Safety Glasses: Always protect yourself when working around electrical components.
Once you have your tools, let’s get started.
Step 1: Check for Error Codes
Before doing any physical checks, it’s a good idea to plug in an OBD-II scanner to check for error codes. The codes will tell you if the crankshaft position sensor is the issue and if there are any specific problems, like a short circuit or faulty sensor.
Some common codes related to a crankshaft position sensor problem are:
- P0335: Crankshaft Position Sensor “A” Circuit Malfunction
- P0336: Crankshaft Position Sensor Range/Performance Problem
- P0337: Crankshaft Position Sensor “A” Circuit Low Input
These codes are a great starting point and will give you a more precise idea of what needs fixing.
Step 2: Inspect the Wiring and Sensor
Now, let’s get hands-on. Pop the hood and locate the crankshaft position sensor. This is usually near the crankshaft or flywheel, depending on your vehicle make and model. Once you’ve found it, visually inspect the wiring for any signs of damage, such as fraying, corrosion, or burns.
If the wiring looks good, try gently wiggling it to see if there are any loose connections that could cause a short circuit.
Step 3: Test the Sensor’s Electrical Current
This is where the multimeter comes in. Set your multimeter to the “voltage” setting, and connect the probes to the sensor’s wiring. You should get a reading of a steady voltage if the sensor is working correctly. If the voltage is erratic, too high, or too low, this could indicate a short circuit or faulty sensor.
Step 4: Test the Grounding
Check if the sensor’s grounding wire is properly connected. If the ground connection is weak or corroded, it could cause the sensor to malfunction. A poor ground connection often leads to electrical shorts, so ensure it’s clean and tightly attached.
Step 5: Check for Continuity in the Wiring
For this, you’ll need the multimeter again. Set it to measure continuity and place one probe at each end of the wiring. If the multimeter shows no continuity or an open circuit, the wire may be broken, and that could be the cause of the short.
Step 6: Inspect the Sensor for Internal Damage
If the wiring and grounding check out but you’re still having issues, it might be time to test the sensor itself. Using the multimeter, measure the sensor’s resistance. If the resistance is out of range, the sensor is likely faulty and needs replacing.
How to Fix and Prevent Future Short Circuits
Now that you’ve diagnosed the short circuit in your crankshaft position sensor, it’s time to tackle the repair. While some issues can be fixed easily, others might require part replacement. Let’s explore the ways to fix the problem and prevent it from happening again.
Step 1: Replace Damaged Wires
If you’ve found that the wiring is damaged, frayed, or corroded, the solution is simple: replace the wiring. Cut out the damaged section and strip the insulation back carefully, then reattach the wires using electrical connectors or soldering. Be sure to match the wires exactly, and insulate them properly to avoid future issues.
Step 2: Replace the Crankshaft Position Sensor
If the sensor itself is faulty and cannot be repaired, it’s time for a replacement. Crankshaft position sensors are fairly easy to replace in most vehicles, and they’re relatively inexpensive.
To replace the sensor:
- Disconnect the battery to prevent any electrical issues.
- Remove the old sensor using the appropriate tools.
- Install the new sensor in the same location, ensuring it’s seated correctly.
- Reconnect the wiring and test the sensor with your multimeter to ensure proper functioning.
Step 3: Clean Corroded Connections
If corrosion is the problem, use a wire brush or contact cleaner to clean the wiring and connectors. Make sure to remove all traces of corrosion, as even a small amount can cause electrical issues.
Step 4: Install a Fuse or Relay
Sometimes, a short circuit occurs because there’s too much power running through the system. Installing a fuse or relay can help protect the circuit from future damage. This is a good preventive measure to avoid short circuits and electrical overload.
Step 5: Prevent Future Issues
To prevent future short circuits in your crankshaft position sensor, consider the following tips:
- Regular Inspections: Regularly check the wiring, sensor, and connections for signs of wear and tear.
- Avoid Moisture: If you live in a rainy area, make sure your engine’s electrical components are sealed properly to keep moisture out.
- Quality Parts: Always use high-quality replacement parts for better durability and reliability.
By following these tips, you’ll be able to keep your crankshaft position sensor in top condition and avoid future short circuits.
I hope this guide has helped you understand how to repair a short circuit in your crankshaft position sensor. With the right tools and a little patience, you can easily get your engine back to running smoothly.
Frequently Asked Questions
Is it difficult to replace a crankshaft position sensor?
Replacing a crankshaft position sensor is relatively straightforward, but it can vary depending on your vehicle. Most people can handle it with basic tools and patience.
Can I drive with a shorted crankshaft position sensor?
It’s not advisable to drive with a shorted crankshaft position sensor, as it can cause poor engine performance and potentially lead to further damage to the engine.
Do I need to reset the ECU after replacing the crankshaft position sensor?
Yes, after replacing the sensor, it’s often necessary to reset the ECU to ensure it recalibrates and recognizes the new sensor.
Is it possible to fix a short circuit in the crankshaft position sensor without replacing it?
In some cases, you can fix the wiring or clean the connections, but if the sensor itself is damaged, it will need to be replaced.
Can a short circuit in the crankshaft position sensor cause the engine to stall?
Yes, a short circuit in the sensor can cause the engine to stall, as it disrupts the timing of the fuel injection and ignition.
Do I need to replace the entire wiring harness for a shorted sensor?
Not always. If the short circuit is limited to one wire, replacing just that section might be sufficient.
Is there a way to prevent short circuits in the crankshaft position sensor?
Regular maintenance, inspecting wiring, and using high-quality parts can help prevent short circuits in the crankshaft position sensor.
Can a faulty crankshaft position sensor affect other engine components?
Yes, a faulty sensor can affect the performance of other components like the fuel injectors, ignition coils, and overall engine timing.